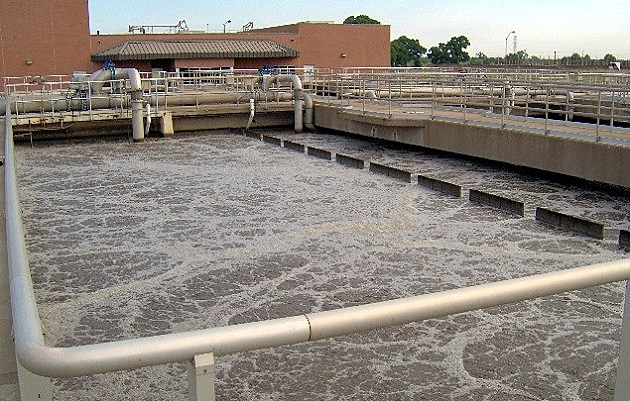
River Road Wastewater Plant
City of Wichita Falls
By Mike Hendren July 20, 2016 5:00 PM
After a two week investigation, the City of Wichita Falls has released its findings on the accident that led to the death of one city employee and has left a second in very critical condition. The investigation concluded that Daniel Arrendondo and David Sheppard, both maintenance mechanics for the City of Wichita Falls, failed to wear breathing apparatus when they entered a basement of the facility for a second time on July 2.
Arrendondo and Sheppard were both trained in the use of the equipment and safety protocols, but for unknown reasons, both chose to enter the basement without the gear, even after making a special trip to retrieve new air tanks. Arrendondo died on July 10. Sheppard, at last report, remained hospitalized in very critical condition.
Below is the full text of the press release from the City of Wichita Falls detailing the findings of the investigation.
On July 2, 2016, at 2:42 p.m., a sensor alarm notified plant operators that more than ½” of liquid was on the floor of Primary #2 basement. Senior maintenance mechanic David Sheppard and his assistant, maintenance mechanic Daniel Arredondo, were on-call and responded to repair a valve on primary pump 223 that was causing wastewater sludge to leak onto the floor. The mechanics were informed by the operators that it smelled “gassy” in the area. The plant operators report that they saw David Sheppard and Daniel Arredondo put on Self-Contained Breathing Apparatus (SCBA) tanks as a precaution before entering the basement to make repairs at or around 3:30 p.m.
At 4:00 p.m. a plant operator visited with the mechanics outside of the basement area and the mechanics were wearing SCBA tanks at that time. They informed the operator at that time that they were going to the storage area to pick up new air tanks for the SCBAs as their air was running low. The plant operator left to perform his rounds at the plant and returned to the primary pump # 2 at 5:00 p.m. At that time, he found both employees unconscious, they were not wearing their SCBA’s, and the air tanks were located in boxes at the top of the stairs.
The operator who found the employees contacted another employee at the plant to inform him that the two maintenance employees were unconscious in Primary Basement #2, and requested that emergency responders be contacted. EMS and Fire EN2 were dispatched at 5:01 p.m., Squad 2 at 5:04 p.m., and Haz-Mat EN5 at 5:10 p.m.; Police and Risk Management were notified at 5:25 p.m.
First responders were on-site at 5:06 p.m. Daniel Arredondo was found at the bottom level at the foot of the staircase and David Sheppard was found on the first landing of the stairs. The employees were extracted from the basement by first responders soon thereafter and transported to the hospital.
Relief maintenance crews that were called in to finish the repairs had a gas monitor that registered 509ppm hydrogen sulfide. The remainder of the repairs took approximately 10 minutes once started. Periodic readings of hydrogen sulfide levels were taken. 0 PPM was not reached until the mechanics left at 11:30 p.m.
During the investigation, it was determined that Mr. Sheppard and Mr. Arredondo did not take any air quality measurements in the area and did not complete the initial checklists for the SCBAs.
The flow to the valve and the air compressor responsible for moving the sludge through the pipe were turned off prior to the mechanics’ arrival, as per best practice. In addition, all reverse flow valves were closed so that sludge or gas could not flow backwards.
Per-conversation with Harold Burris Waste Water Treatment Superintendent, it was considered unusual for there to be hazardous levels of hydrogen sulfide in the area in which the employees were working; however, there have been occasions in the past where conditions required employees to utilize Personal Protective Equipment (PPE) for maintenance work in this area. The ventilation, both outgoing and intake, was functioning normally. The door to the building was open and there was less than 1” of sewage on the floor of the basement. The source of the H2S was determined to be the sludge that came out of the valve and what was present in the pipes when the valve was open for repairs.
The cause of the release of sewage was built up pressure in the valve that traps debris. These valve traps must be cleaned bi-weekly to avoid pressure build-up. Maintenance work had been completed on valve 223 the day before. In this instance, pressure had built up in the valve, causing the bolt to shear off. According to superintendent Harold Burris, this has occurred 6 times in the past 12 months and is a routine maintenance task. Proper procedures were followed by turning off the valve, and turning off air condenser that feeds the line running through the valve that was being worked on.
Training records for PPE, hazardous materials, and Hazard Communications Act are available. Mr. Arredondo and Mr. Sheppard both attended hazardous materials training most recently on February 3, 2016. This course covered safe handling of hazardous chemicals, PPE, first aid with respect to hazardous chemicals, general clean-up safety, acute and chronic effects of exposure, locations of hazardous chemicals in the workplace, and awareness of the hazardous chemical lists. Training over hydrogen sulfide was included in this course. Additionally, both Mr. Sheppard and Mr. Arredondo had received periodic training on wastewater treatment wastewater plant operations.
Conclusions:
We have concluded that the employees were properly trained on the use of PPE and the maintenance task being performed. It was further determined that the employees were using PPE at the beginning of tasks; however, when found at the scene of the accident they were not wearing the equipment. It is unknown why the employees removed the PPE, and this information would not be available unless we were able to speak with the employees directly. It has also been concluded that the environment the employees entered contained a level of hydrogen sulfide gas that was outside of the norm of levels encountered while performing this task. As of the date of this report, the City of Wichita Falls city management is in the process of identifying third parties to assist in the follow-up of this investigation and determination thereof, and is conducting internal investigations.
A review of the permits for all categorical industrial users of the City’s wastewater collection and treatment systems and determined that none have large sulfur content in their discharges to the City’s treatment facilities. Interviews with each of the City’s industrial users for any possible upsets in their pre-treatment process, and any possibility of discharges containing elevated sulfur content, have been made and it was determined that none were found. A review of the Industrial User Surveys (125 industries) that were completed for the entire City of Wichita Falls from the end of April through the first of May this year did not find any industries that use sulfur in a production process.
The City is in the process of obtaining the services of independent consultants to assist in determining, if possible, the cause of the excessive levels of Hydrogen Sulfide in the basement area on the date of the incident. Dr. Leonard Ripley P.E of Freese and Nichols Engineering, an industry specialist in biological wastewater treatment and sludge digestion and disposal, is currently assisting in this process.
The Public Works Department has contacted several federal and state agencies to request a separate investigation into the incident as well as an assessment of the City’s safety training, equipment and protocols. One agency contacted was the National Institute of Safety and Health (NIOSH). This agency declined to investigate as they do not have an agreement with the State of Texas to perform work within the state. OSHA also does not have jurisdiction over municipalities and, therefore would not investigate. The Public Work’s staff contacted Texas Engineering Extension Service (TEEX), an agency that performs extensive safety training for municipalities. This organization also declined to investigate the incident. However TEEX referred the staff to a Mr. Luis Villanueva, an instructor for TEEX, and former OSHA employee, who agreed to perform an incident investigation and review of the safety programs for the City Wastewater Treatment Plant. Mr. Villanueva was at treatment plant on July 9th. During his review, Mr. Villanueva interviewed staff and visited the incident area. Plant staff provided him with training information, certifications, the incident report form the Fire Department and Police Department, as well as other information he requested. His final report is expected to be delivered within a few weeks.
On Tuesday, July 12, an investigator from the Department of Health and Human Services, Environmental and Consumer Safety Region conducted a workplace investigation at the River Road wastewater treatment plant facility. The investigator found no issues with the plant’s safety training, equipment and protocols as it relates to the Texas Hazards Communications Act. The City should be receiving a written report to that effect.
The Waste Water Treatment department has also implemented the following precautionary measures for the duration of the investigation:
o Testing the air quality in the affected area every 2 hours
o Requiring employees to carry gas detectors into areas where hydrogen sulfide could be present
o Planning the installation of permanent gas detection alarms in the areas in which this occurred and other similar areas in the plant.
o Plant superintendent has held meetings with employees to review the dangers of hydrogen sulfide gas and reiterated to them the use of PPE and their training.
o Plant Superintendent and the Operations Supervisor have reviewed training materials and manuals for adequacy. All were found to be adequate.