CDC calls for protections for coffee workers, others in food industry
Raquel Rutledge , Milwaukee Journal Sentinel 4:23 p.m. CDT November 1, 2016
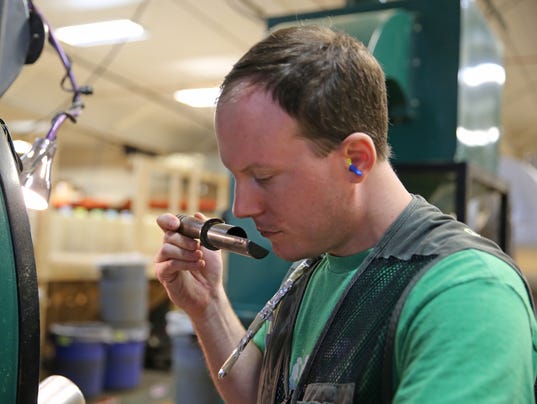
(Photo: Mike De Sisti / Milwaukee Journal Sentinel)
Calling the risks of contracting permanent or deadly lung disease “serious,” the CDC finalized a warning Monday to those in the coffee, popcorn and other food and beverage making businesses: Beware of diacetyl.
The chemical occurs naturally in coffee roasting and is released in higher concentrations when the beans are ground or storage bins are opened. It’s also produced synthetically and added to all kinds of foods and drinks to impart a buttery, creamy flavor.
While the FDA has deemed diacetyl safe to consume in trace amounts, inhaling it has proven deadly.
“Employers need to understand what steps can be taken to protect the health of their workers,” said Christina Spring, spokeswoman for the National Institute of Occupational Safety and Health, the research arm of the U.S. Centers for Disease Control and Prevention.
NIOSH couldn’t say how many workers might be exposed to diacetyl nationwide, but numbers from the U.S. Bureau of Labor Statistics show as many as 600,000 people work in the coffee industry alone.
Diacetyl attacks and inflames the lung’s tiniest airways leading to scar tissue build-up that blocks airflow. Called bronchiolitis obliterans, the damage is permanent. Exposure can also cause eye and skin irritation and other respiratory illness.
In the early and mid-2000s, scientists linked diacetyl to several deaths and hundreds of injuries to workers in microwave popcorn factories in Missouri, California, Illinois and elsewhere. Dozens of public health experts at the time petitioned the government to step in and issue regulations, noting “compelling epidemiologic and toxicological evidence linking exposure to diacetyl to severe respiratory impairment and disease.”
NIOSH drafted recommendations for exposure limits in 2011 but never finalized them and the U.S. Occupational Safety and Health Administration, the agency tasked with overseeing workplace safety in the United States, never passed regulations.
The issue gained steam last year in the wake of a Milwaukee Journal Sentinel investigation that examined how five workers in a Texas coffee processing plant contracted debilitating lung disease linked to diacetyl and exposed how workers in cafes and roasteries that don't use added flavors are also at risk.
Monday's action is dubbed a “criteria document.” The 426-page report suggests workers not be exposed to more than a time-weighted average of 5 parts per billion of diacetyl during an 8-hour day, over a 40-hour work week. Researchers calculated the exposure rate to allow no more than one worker per 1,000 to become ill in the course of a 45-year work life.
The recommendations are more stringent than those called for by other groups who have published guidelines for diacetyl exposure, such as the American Conference for Governmental Industrial Hygienists. In 2012, that group suggested workers be exposed to no more than 10 ppb over an 8-hour time-weighted-average.
Lauralynn McKernan, who helped spearhead the recommendations for NIOSH, said different groups use different criteria when setting policy.
NIOSH considers three main factors when proposing exposure limits: Quantitative analysis, meaning studying all the evidence-based, actual health risks; analytical analysis, which is how exposure is measured; and engineering feasibility, which looks at the ability for industry to achieve reduced exposures.
"We carefully considered all of that," said McKernan, associate director for science with NIOSH's Division of Surveillance, Hazard Evaluations and Field Studies.
The agency responded to every public comment and considered all stakeholder concerns, she said. The cost to industry to implement engineering controls and other mitigating policies and procedures, however, was not a factor in the risk equation, McKernan said.
In addition, NIOSH's recommendation factors in the latest research, citing studies published as recently as 2015 and 2016. And it includes references to naturally occurring diacetyl.
"When it comes to natural or artificial diacetyl, diacetyl is diacetyl," McKernan said. "We're focused on getting diacetyl exposures down."
Recommendations, not regulations
The recommendations are strictly that: recommendations.They carry no regulatory teeth. Officials with OSHA did not immediately respond to a request for comment on how NIOSH's conclusions about the chemicals might influence the agency's oversight of food and beverage worker safety.
The document also includes recommended exposure limits for 2,3-pentanedione — a chemical cousin to diacetyl that also occurs naturally in coffee and has been used by many companies as a replacement. Studies have found 2,3-pentandione to be as toxic as diacetyl.
The recommendations encourage employers to test the air in their roasting and manufacturing facilities for diacetyl and 2,3 pentanedione and to take precautions, such as improving exhaust and ventilation. They also stress the importance of conducting breathing tests and monitoring the health of everybody in work environments that contain diacetyl and 2,3-pentandione.
In addition to major food manufacturing, the recommendations apply to large commercial coffee processing operations as well as small cafes with only one or two roasting ovens.
An investigation by the Milwaukee Journal Sentinel last year found concentrations of diacetyl and 2,3-pentainedione at two mid-size coffee roasteries in Wisconsin exceeded the NIOSH limits.
The investigation also detailed how five workers in a Texas coffee plant became gravely ill with bronchiolitis obliterans. One was put on the waiting list for a lung transplant.
The finalized recommendations do not apply to roasting, grinding or brewing coffee at home. They do not address diacetyl in electronic cigarettes or vape juice, where the Journal Sentinel also found the chemicals. The exposure limits are designed for occupational environments only.
The National Coffee Association, which represents the estimated $74 billion U.S. coffee industry, denies diacetyl is a serious threat.
"We maintain that the levels NIOSH is recommending are exceedingly and unnecessarily low," said Joseph DeRupo, spokesman for the association. "We review the science as well and are reviewing the science day in and day out and are watching for potential hazards and addressing them as need be."
The Journal Sentinel's investigation found some of the largest coffee processors in the United States don't test the air for diacetyl or provide medical surveillance for their workers.