The five men who died were found in the “dog house,” a control room located near the drilling platform. The Oklahoma Department of Emergency Management identified them as Roger Cunningham, 55, of Seminole; Josh Ray, 35, of Fort Worth, Texas; Cody Risk, 26, of Wellington, Colo.; Matt Smith, 29, of McAlester, and Parker Waldridge, 60, of Crescent.
July 30, 2018
U.S. Department of Labor Cites Three Companies in Oklahoma
After Five Employees Fatally Injured by Explosion and Fire
OKLAHOMA CITY, OK–
The U.S. Department of Labor’s Occupational Safety and Health Administration (OSHA) has cited Patterson-UTI Drilling, Crescent Consulting LLC, and Skyline Directional Drilling LLC for exposing employees to fire and explosion hazards after five employees suffered fatal injuries.
The explosion and fire occurred on a Patterson-UTI drilling rig near Quinton, Oklahoma. OSHA cited Patterson-UTI and Crescent Consulting for failing to maintain proper controls while drilling a well, inspect slow descent devices, and implement emergency response plans. OSHA cited all three companies for failing to ensure that heat lamps in use were approved for hazardous locations. The three companies face penalties totaling $118,643, the maximum allowed for violation of the OSHA standards.
“These employers failed to properly control hazards involved in oil and gas extraction activities, and the result was tragic,” said OSHA Oklahoma City Area Office Director David Bates. “Employers are required to monitor their operations to ensure workplace health and safety procedures are adequate and effective.”
The companies have 15 business days from receipt of the citations and penalties to comply, request an informal conference with OSHA’s area director, or contest the findings before the independent Occupational Safety and Health Review Commission. The citations can be viewed here, here, and here
Under the Occupational Safety and Health Act of 1970, employers are responsible for providing safe and healthful workplaces for their employees. OSHA’s role is to help ensure these conditions for America’s working men and women by setting and enforcing standards, and providing training, education and assistance. For more information, visit http://www.osha.gov.
=========================
January 25, 2018
Authorities Investigating Oklahoma Rig Explosion, Deadliest U.S. Drilling Accident In Years
Joe Wertz
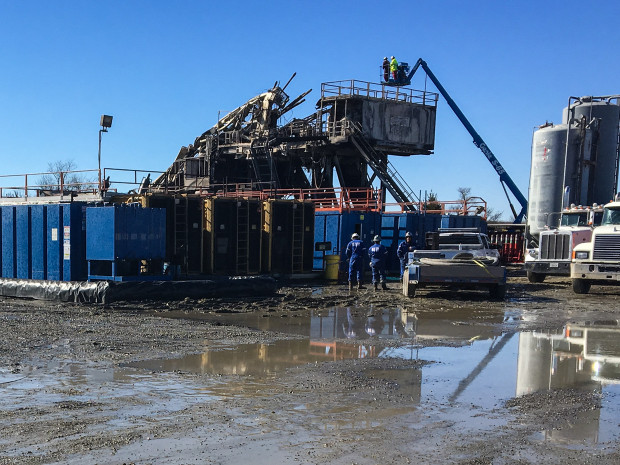
Oklahoma Corporation Commission
Inspectors and emergency crews surveying damage at Patterson-UTI's rig 219, which exploded and caught fire Jan. 22.
Federal and state authorities are investigating the cause of the deadly explosion and fire at a natural gas drilling rig in southeastern Oklahoma on Monday. Five workers died in what appears to be one of the country’s deadliest onshore drilling accidents.
The well site, located near the town of Quinton, 100 miles south of Tulsa, was operated by Oklahoma City-based Red Mountain Energy. Patterson-UTI Energy, of Houston, owns and operates the drilling rig, which exploded and caught fire about 8:45 a.m.
The cause of the explosion and fire is not yet known. The Occupational Safety and Health Administration and the Chemical Safety Board are investigating, as is the Oklahoma Corporation Commission, the state’s oil and gas regulator.
A day after the explosion, Oklahoma’s Supreme Court struck down a portion of the state’s workers compensation law, ruling 8-0 that oil and gas companies can be sued when workers are injured or killed. Oklahoma law holds operators responsible for well site safety, not contract drillers or oil-field service companies.
A preliminary report from a commission investigator found the fire that engulfed the rig was fed by an “uncontrolled gas release.” A rig worker attempted to activate a device known as a blowout preventer to shut off the well but was unable to, the inspector reported.
The fire at the wellhead kept emergency crews at bay for hours and created a black plume of smoke visible for miles. One worker who escaped with burns was taken by helicopter to a hospital and later released; sixteen other workers who fled the burning rig were uninjured.
“From what I was told from many of the survivors, there was an explosion, they heard a loud boom, they seen fire and they ran,” Pittsburg County Sheriff Chris Morris said. “Everybody was trying to survive.”
The five men who died were found in the “dog house,” a control room located near the drilling platform. The Oklahoma Department of Emergency Management identified them as Roger Cunningham, 55, of Seminole; Josh Ray, 35, of Fort Worth, Texas; Cody Risk, 26, of Wellington, Colo.; Matt Smith, 29, of McAlester, and Parker Waldridge, 60, of Crescent.
Tony Say, a founder of Red Mountain Energy, told reporters Tuesday the small energy company was “absolutely devastated” by the accident.
“Our thoughts are with those whose lives have been impacted beyond words by this tragedy. You’ll be in our prayers over the coming days and weeks,” he said. “Our priority, sincerely, is the people who have been affected and the safety of those who will be called upon to work the well site and investigate.”
In a statement, Patterson-UTI President and CEO Andy Hendricks said his employees were “deeply saddened” and pledged a thorough investigation of the accident.
“There is nothing more important to us than the safety of our employees and others we partner with in the field. Tonight, our thoughts and prayers go out to all those affected and their loved ones.”
Patterson-UTI has struggled for years with one of the worst safety records in the drilling industry, OSHA data show. A 2008 report from the U.S. Senate Health, Education, Labor and Pensions subcommittee identified 12 deaths at Patterson-UTI drilling sites in Texas alone. Inspections of drilling sites the company operates in Oklahoma and other states have turned up numerous violations, OSHA data show.
Drilling is a dangerous job. At least 60 workers in Oklahoma have died working for energy companies or on the job at oil and gas drilling sites from 2011-2016, data from the U.S. Bureau of Labor Statistics show. In 2012, a sharp rise in deadly oil-field accidents led to a voluntary statewide shutdown of drilling activity so rig work crews could review safety standards and procedures.