Fire damages Idaho grain elevator May 14, 2013 - by Laura Lloyd
CRAIGMONT, ID. — Insurance adjusters were headed to the smoldering aftermath of a major May 12 fire at a chick pea storage facility owned by Hinrichs Trading and three adjoining elevators owned by Columbia Grain that held a variety of crops ranging from peas and lentils to barley.
The report by insurers will help nail down the cause, the price tag — expected to be in the millions of dollars — and the time frame required to rebuild from the ground up. Until then, the owners will have to figure out how to compensate for the loss of a combined storage capacity of 700,000 bus, although neither facility was full when the fire started.
Max Hinrichs, vice-president of Hinrichs Trading, Pullman, Wash., said the buildings, located in a remote part of the small Idaho town of Craigmont, had probably been burning for a few hours before being discovered. He said his fourth-generation family business specializes in growing and selling chick peas (also called garbanzo beans) and is the largest chickpea-only company of its kind in the United States. The cause of the fire was unknown, he said, but he noted that garbanzo beans are not known for being particularly combustible when stored.
He said a railroad track separated his storage elevator and warehouse from the three Columbia Grain elevators, and the fact that the fire managed to spread across the tracks attested to its force. No one was hurt, but destruction of the Hinrichs elevator and adjoining warehouse and Columbia Grain elevators was assumed to be total.
Mr. Hinrichs said he foresaw little disruption to his business because the company has storage facilities in Pullman that could be utilized to hold the chick peas that normally would have been stored in Craigmont.
Randy Olstad, a regional manager for Columbia Grain, a subsidiary of Marubeni, Japan, with assets throughout the Northwest United States, said he could not comment on either the likely cause or the cost to rebuild the three cribbed elevators until after insurance professionals assessed the situation. He said the elevators and their contents remained in a smoky, smoldering state two days after the fire began.
===============
AUGUST 29, 2016
WILSON, NC
Firefighters battle blaze in Wilson grain elevator at 1711 Hwy 301 Wilson, NC 27893. The grain storage facility belongs to the Southeastern Grain Company.
=================
Welcome to Southeastern Grain Company
Southeastern Grain Company, LLC (SGC) is a rapidly evolving feed ingredient based enterprise in North and South Carolina. SGC is young in years but old at heart. Our experience and facilities span generations and we will continue to serve the coming generations in agriculture. We originate local grain and oilseeds from producers into ten strategically located SGC granaries and numerous outside feed manufactures and processors. This network ensures our customers efficiency when it comes to drying or receiving grain. A key to our success is the passion each employee shares for the agricultural communities they serve and respecting the hard work put into producing the grain we handle.
We value our long term relationships and are committed to investing in the communities in which we operate. Superior service and flexibility combined with excellent marketing tools and a drive to differentiate ourselves within the industry enables us to seek maximum profit for our producers. SGC facilities offer a tremendous value in risk management and navigating the local and global volatile agricultural markets.
==============
What are grain handling facilities?
Grain handling facilities are facilities that may receive, handle, store, process and ship bulk raw agricultural commodities such as (but not limited to) corn, wheat, oats, barley, sunflower seeds, and soybeans. Grain handling facilities include grain elevators, feed mills, flour mills, rice mills, dust pelletizing plants, dry corn mills, facilities with soybean flaking operations, and facilities with dry grinding operations of soycake.What are the hazards in grain handling facilities?
The grain handling industry is a high hazard industry where workers can be exposed to numerous serious and life threatening hazards. These hazards include: fires and explosions from grain dust accumulation, suffocation from engulfment and entrapment in grain bins, falls from heights and crushing injuries and amputations from grain handling equipment.Suffocation is a leading cause of death in grain storage bins. In 2010, 51 workers were engulfed by grain stored in bins, and 26 died-the highest number on record, according to a report issued by Purdue University (PDF) Suffocation can occur when a worker becomes buried (engulfed) by grain as they walk on moving grain or attempt to clear grain built up on the inside of a bin. Moving grain acts like "quicksand" and can bury a worker in seconds. "Bridged" grain and vertical piles of stored grain can also collapse unexpectedly if a worker stands on or near it. The behavior and weight of the grain make it extremely difficult for a worker to get out of it without assistance. OSHA has sent notification letters to approximately 13,000 grain elevator operators warning the employers to not allow workers to enter grain storage facilities without proper equipment, precautions (such as turning off and locking/tagging out all equipment used so that the grain is no being emptied or moving into the bin) and training.
Grain dust explosions are often severe, involving loss of life and substantial property damage. Over the last 35 years, there have been over 500 explosions in grain handling facilities across the United States, which have killed more than 180 people and injured more than 675. Grain dust is the main source of fuel for explosions in grain handling. Grain dust is highly combustible and can burn or explode if enough becomes airborne or accumulates on a surface and finds an ignition source (such as hot bearing, overheated motor, misaligned conveyor belt, welding, cutting, and brazing). OSHA standards require that both grain dust and ignition sources must be controlled in grain elevators to prevent these often deadly explosions.
Falls from height can occur from many walking/working surfaces throughout a grain handling facility. Examples of such surfaces include (but are not limited to) floors, machinery, structures, roofs, skylights, unguarded holes, wall and floor openings, ladders, unguarded catwalks, platforms and manlifts. Falls can also occur as workers move from the vertical exterior ladders on grain bins to the bin roof or through a bin entrance.
Mechanical equipment within grain storage structures, such as augers and conveyors, present serious entanglement and amputation hazards. Workers can easily get their limbs caught in improperly guarded moving parts of such mechanical equipment.
Storage structures can also develop hazardous atmospheres due to gases given off from spoiling grain or fumigation. Workers may be exposed to unhealthy levels of airborne contaminants, including molds, chemical fumigants (toxic chemicals), and gases associated with decaying and fermenting silage. Fumigants are commonly used for insect control on stored grain and many have inadequate warning properties. Exposure to fumigants may cause permanent central nervous system damage, heart and vascular disease, and lung edema as well as cancer. These gases may result in a worker passing out and falling into the grain, thus becoming engulfed and suffocating or otherwise injuring themselves.
What can be done to reduce the hazards in grain handling facilities?
On August 4, 2010 and again on February 1, 2011, OSHA issued warning letters to the grain handling industry following a series of incidents including the recent suffocation of 2 teenagers in Illinois grain elevator. In response to the rising number of workers entrapped and killed in grain storage facilities, OSHA has also issued a new fact sheet, Worker Entry Into Grain Storage Bins (PDF*) in August 2010 for workers and employers emphasizing the hazards of grain storage bin entry and the safe procedures that all employers must follow. Additionally, OSHA issued a safety and health information bulletin (SHIB) entitled, Combustible Dust in Industry: Preventing and Mitigating the Effects of Fire and Explosions, and a Hazard Alert: Combustible Dust Explosions (PDF*) fact sheet.The control of worker's exposure to hazards in grain handling facilities are addressed in the OSHA standard for grain handling facilities (29 CFR 1910.272), as well as in other general industry standards. These standards reduce the risk to workers by requiring that employers follow established, common sense safety practices when working in grain handling facilities.
When workers enter storage bins, employers must (among other things):
- Turn off and lock out all powered equipment associated with the bin, including augers used to help move the grain, so that the grain is not being emptied or moving out or into the bin. Standing on moving grain is deadly; the grain can act like "quicksand" and bury a worker in seconds. Moving grain out of a bin while a worker is in the bin creates a suction that can pull the workers into the grain in seconds.
- Prohibit walking down grain and similar practices where an employee walks on grain to make it flow.
- Provide all employees a body harness with a lifeline, or a boatswains chair, and ensure that it is secured prior to the employee entering the bin.
- Provide an observer stationed outside the bin or silo being entered by an employee. Ensure the observer is equipped to provide assistance and that their only task is to continuously track the employee in the bin. Prohibit workers from entry into bins or silos underneath a bridging condition, or where a build-up of grain products on the sides could fall and bury them.
- Train all workers for the specific hazardous work operations they are to perform when entering and working inside of grain bins.
- Test the air within a bin or silo prior to entry for the presence of combustible and toxic gases, and to determine if there is sufficient oxygen.
- If detected by testing, vent hazardous atmospheres to ensure that combustible and toxic gas levels are reduced to non hazardous levels, and that sufficient oxygen levels are maintained.
- Ensure a permit is issued for each instance a worker enters a bin or silo, certifying that the precautions listed above have been implemented.
- Develop and implement a written housekeeping program with instructions to reduce dust accumulations on ledges, floors, equipment and other exposed surfaces.
- Identify "priority" housekeeping areas in grain elevators. The "priority" housekeeping areas include floor areas within 35 feet of inside bucket elevators, floors of enclosed areas containing grinding equipment and floors of enclosed areas containing grain dryers located inside the facility. Dust accumulations in these priority housekeeping areas shall not exceed 1/8th inch. Employers should make every effort to minimize dust accumulations on exposed surfaces since dust is the fuel for a fire or explosion, and it is recognized that a 1/8 inch dust accumulation is more than enough to fuel such occurrences.
- Inside bucket elevators can undergo primary explosions. OSHA's grain handling standard requires that belts for these bucket elevators purchased after March 30, 1988 are conductive and have a surface electrical resistance not exceeding 300 megohms. Bucket elevators must have an opening to the head pulley section and boot section to allow for inspection, maintenance, and cleaning. Bearings must be mounted externally to the leg casing or the employer must provide vibration, temperature, or other monitoring of the conditions of the bearings if the bearings are mounted inside or partially inside the leg casing. These bucket elevators must be equipped with a motion detection device which will shut-down the elevator when the belt speed is reduced by no more than 20% of the normal operating speed.
- Implement a preventative maintenance program with regularly scheduled inspections for mechanical and safety control equipment, which may include heat producing equipment such as motors, bearings, belts etc. Preventive maintenance is critical to controlling ignition sources. The use of vibration detection methods, heat sensitive tape or other heat detection methods can help in the implementation of the program.
- Minimize ignition sources through controlling hot work (electric or gas welding, cutting, brazing or similar flame producing operations).
- Install wiring and electrical equipment suitable for hazardous locations.
- Design and properly locate dust collection systems to minimize explosion hazards. All filter collectors installed after March 1988 shall be located outside the facility or located in an area inside the facility protected by an explosion suppression system or located in an area that is separated from other areas by construction having at least a one hour fire resistance rating and which is located next to an exterior wall vented to the outside.
- Install an effective means of removing ferrous material from grain streams so that such material does not enter equipment such as hammer mills, grinders and pulverizers.
DeBruce Grain Elevator Explosion

A structural failure of the east side truss caused
the bins to collapse down three floors into the center of International
Nutrition's Omaha facility, Jan. 20, 2014. Read news release for more information.

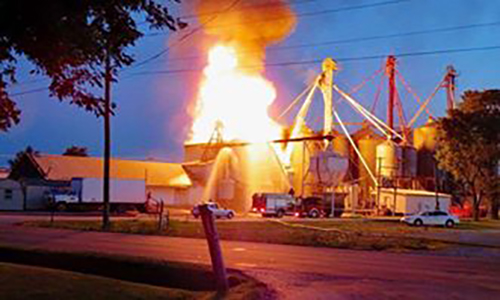
Local News July 19, 2016 Randall
Reports from Unionville state the Putnam County MFA Exchange Elevator burned in a fire today with several fire departments responding to the grain elevator fire on South 23rd Street.
A representative from the state Fire Marshal’s office was to be on the scene at Unionville to begin an investigation regarding the cause of the fire.
The main structure is described as a complete loss. Smoke damage was noted to other nearby buildings.
In a related announcement, a precautionary boil water order was issued today for the entire town of Unionville, effective through Thursday.
The Unionville Republican newspaper, in its edition this week, reported the business had been undergoing construction work involving an expansion and renovations.
KTTN would like to express appreciation to Dennie Sheehan for the photos that accompany this story.
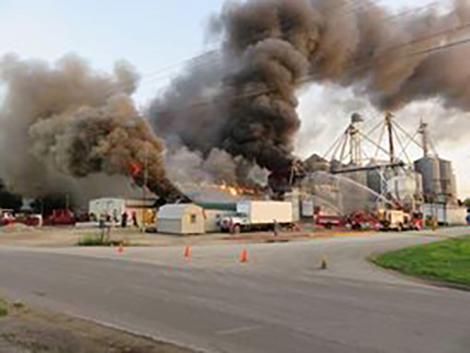
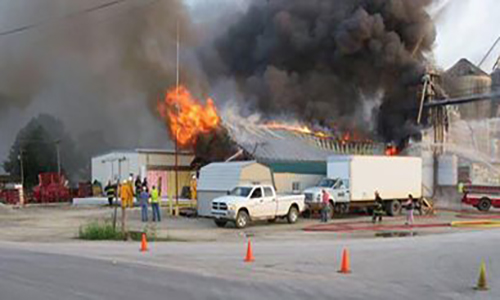
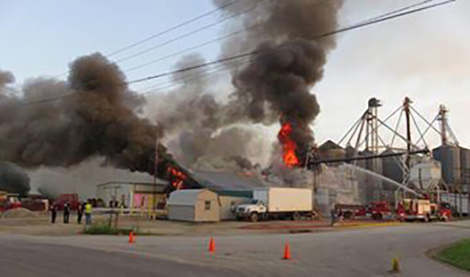
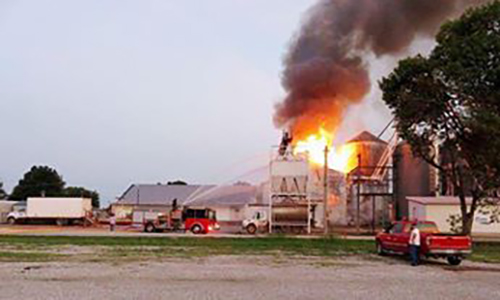
Fire destroys grain elevator in Unionville, investigation underway
Elizabeth Orosco | July 20, 2016
UNIONVILLE, Mo.– Early Tuesday morning, fire crews battled a blaze at the MFA Exchange & Elevator in Unionville, Missouri.
Fire Chief Tim Montgomery told KMZU one person was taken to the hospital, suffering only minor heat exhaustion. Investigation is still underway to determine the cause of the fire.
The structure has been deemed a total loss with several buildings nearby accumulating smoke damage. Chief Montgomery says crews are working hard to clean up the damage and more information will be released as becomes available.
