
(Photo: ASSOCIATED PRESS)
Jeff Mordock, The News Journal
August 20, 2015
DuPont has long been recognized as a safety leader within the chemical industry. Its people train other companies and industries in best practices for environmental and workplace safety.
Now, the company is facing heavy criticism from employee unions and government agencies after a series of high-profile accidents and deaths at plants across the country.
Eight workplace fatalities since 2007, numerous lawsuits, multiple federal regulatory agency investigations and millions of dollars in Occupational Safety and Health Administration fines have some wondering if DuPont's historically good safety record still exists.
In July, OSHA placed DuPont in a program for "severe" violators of workplace safety standards. Severe is the worst category, and companies are placed in it after repeatedly failing to address OSHA violations.
DuPont is the largest of the roughly 450 companies in the severe category. Smaller construction companies comprise the bulk of those businesses.
"That is really huge that DuPont got put into the severe violator program," said Celeste Monforton, a former OSHA analyst and now a professor of occupational health at George Washington University. "The companies on that list are the worst of the worst."
DuPont says the workplace deaths have overshadowed a still-strong safety record. Company representatives are quick to point out that DuPont's workplace injury rate is below average for the chemical industry.
On July 1, DuPont spun off its high-performance chemical units into a new company called Chemours in part to absolve itself from environmental liabilities that could exceed $1 billion.
Even after spinning off Chemours, DuPont must still deal with OSHA and U.S. Chemical Safety Board violations or recommendations. All but one of the plants where worker deaths occurred are still operated by DuPont. Only the Belle, West Virginia, plant, where a worker was killed in 2010 is part of Chemours.

Video detailing a 2010 accident at DuPont in Buffalo
In 2013, DuPont received the Robert W. Campbell Award from the National Safety Council, a 100-year-old, nonprofit corporate safety advocacy group. The Campbell Award is presented annually to the safest company across multiple international business sectors.
Company spokesman Dan Turner said the chemical giant has learned from the incidents and is always working to improve safety. Turner said DuPont has partnered with other companies to reassess workplace safety practices since four workers were killed in 2014 by a gas leak at its La Porte, Texas, facility.
"We have a foundation of world-class safety practices, but consistent with best practices, this tragic incident prompted a hard and broad look at our safety management systems," he said.

Employee unions have also joined the chorus of those criticizing DuPont. The United Steelworkers and International Chemical Workers Union Council, two unions representing DuPont workers, sent a letter this month to company Chief Executive Ellen Kullman threatening to pursue regulatory action against the company. The letter said union safety experts have been barred from reviewing plant conditions.
"We have a right under federal labor laws to see what the hazards are at these plants," Michael Wright, director of Health Safety and Environment for USW, told The News Journal. "That's part of representing our members."
Wright said union experts were barred from investigating DuPont's Niagara Falls plant. He said USW needed a court order from the National Labor Relations Board so inspectors could review the facility. By the time the inspectors finally toured the plant, it was more than a year after the original request, Wright said.
Turner did not respond directly to Wright's allegation.
"DuPont has worked with local and national unions for many years with positive results and we will continue to engage in constructive dialogue with them at our individual sites," he said.
'Gone downhill'
Clay Dugas grew up admiring DuPont, one of the largest employers near the small Texas town where he was raised.
At one point in the 1980s, he recalled one of his neighbors – an employee at the company – injured himself while working on his roof. Even though the accident occurred during the neighbor's off-work time, the company fired the man for practicing unsafe behavior, Dugas said.
Now an attorney in Beaumont, Texas, Dugas says he never imagined he'd one day file a negligence and wrongful death lawsuit against the company he knew as a hallmark for safety.

A contract worker was crushed by falling equipment at DuPont’s Sabine River Works plant in Orange, Texas, on July 24, 2007. Another was crushed by a rail car on Oct. 7, 2011. (Photo: U.S. CHEMICAL SAFETY BOARD)
Dugas is representing the widow of Gilbert Tisnado, one of four DuPont employees killed last year in La Porte. Tisnado died trying to save three co-workers, according to an OSHA investigation.
"DuPont has exchanged being a safety leader to going to the back of the class," Dugas said. "They've been put on OSHA's severe violator list. That shows it's a systemic problem and a changed safety culture."
USW's Wright agreed with Dugas.
"Historically, it is a company with a pretty good safety record," he said. "We think they have gone downhill over the last few years. I don't want to speculate on the causes."

Monforton wonders if DuPont's reputation for stringent safety requirements was always illusory.
"The only reason we know what's going at DuPont right now is because OSHA has been going into its plants," she said. "OSHA doesn't get into these facilities very often, and I wonder how often they had been to DuPont plants before the fatalities occurred."
Parry Norling, a former health and safety director at DuPont, countered Monforton's assertion. Norling retired in 1998 after 33 years with the company.
"Safety was very important because DuPont knew its ability to safely handle hazardous materials gave the company a competitive advantage," he said. "DuPont really worked at safety."
DuPont required employees to take safe driving courses, and desk pencils were banned because they could roll off and cause someone to trip, Norling recalled. He said he was able to save his young son's life after the child swallowed a poisonous plant because of his DuPont training.
Chemical Safety Board Chairman Rafael Moure-Eraso praised DuPont's history of preventing workplace injuries. In written testimony submitted in December to a joint meeting of two U.S. Senate committees, Moure-Eraso said, "If it can happen at DuPont, I would submit it can happen anywhere."
DuPont's reputation for safety extends to a company unit, dubbed Sustainable Solutions, that trains other companies in workplace and environmental safety.
Sustainable Solutions has worked with more than 1,700 clients in 100 countries, according to Turner. Clients in the mining industry have seen their injury rates decline by as much as 60 percent over a two-year period, while an oil company client saw a 92 percent decrease in fatalities within two years after working with DSS, Turner said.
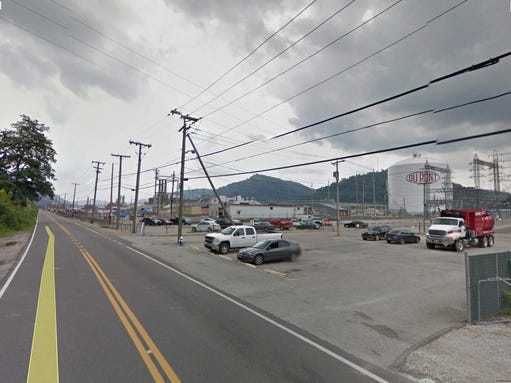
An employee at DuPont’s Belle, West Virginia, facility died after exposure to phosgene, a chemical used as a weapon in World War I, on Jan. 23, 2010. (Photo: U.S. CHEMICAL SAFETY BOARD)
A blow to DuPont's reputation could have a real impact on its bottom line. Sustainable Solutions generated $3.9 billion in 2014, according to the company's annual report.
Monforton said that unit's performance has helped DuPont avoid scrutiny about its own safety record.
"They are selling this safety program to other companies, but the emperor had no clothes," she said. "It's extremely disturbing."
Turner did not respond directly to Monforton's comment, but did emphasize the company cooperates and communicates with regulatory agencies.
Fatalities, lawsuits and investigations
Between 1995 and 2007, one DuPont employee died on the job, according to a review of OSHA documents. The worker, an employee of then-DuPont subsidiary ConocoPhillips, was killed after an oil refinery explosion in Westlake, Louisiana.
Since 2007, eight workers have died in five incidents at DuPont worksites:
• July 24, 2007: Contract worker Lonnie LaFleur was crushed by falling equipment at DuPont's Sabine River Works plant in Orange, Texas.
• Jan. 23, 2010: An employee at DuPont's Belle, West Virginia, facility died after exposure to phosgene, a chemical used as a weapon in World War I.
• Nov. 9, 2010: A worker at the Yerkes Plant in Tonawanda, New York, was killed when a 10,000-gallon slurry tank exploded.
• Oct. 7, 2011: A contract worker was crushed by a rail car at the Sabine River Works plant.
• Nov. 15, 2014: Four workers were killed by methyl mercaptan, a toxic gas used to make insecticides, released at DuPont's LaPorte, Texas plant.

A 2011 video on three DuPont accidents in Belle, WV
"To some degree, bad luck happens," said John Mendeloff, a professor at the University of Pittsburgh, who has authored two books on workplace safety. "But DuPont has had several important disasters, and the investigations in those cases did seem to indicate failings in the safety management systems."
Turner said DuPont is cooperating with both the OSHA and CSB investigations into the LaPorte incident.
"We will learn from this incident, share the critical lessons from it and do all that is necessary to ensure that such an event never happens again," he said.
OSHA fines have increased in recent years, according to data on the agency's website. DuPont paid $57,749 in fines to the regulatory agency between 2000 and 2006. Since 2007, OSHA has levied $640,861 in fines.
Thomas Fuller, director of the health sciences department at the University of Illinois, said OSHA does not punish companies for violations as sternly as other federal agencies such as the Environmental Protection Agency. OSHA fined DuPont $372,000 for the LaPorte tragedy. DuPont, which is valued at $66.7 billion, is contesting those fines.
"Giving a million dollars to the widow of a dead worker is not a lot of money for DuPont," he said. "When we start talking billions, then it will make a difference."
DuPont paid $745 million in 2012 to settle a lawsuit filed by Koch Industries Inc. Koch acquired DuPont's textiles and interiors business, now Invista, for $4.4 billion in 2012, but alleged in legal papers the 12 plants it assumed in the transaction suffered from safety and environmental issues. Benzene, a carcinogen, had leaked from one plant and in others it eroded chemical tanks, posing an explosion threat.
The lawsuit alleged DuPont assured Koch the plants were in compliance with environmental and safety standards. But once the transaction was complete, the EPA discovered 687 violations at the facilities. Koch claimed in court documents the cleanup cost $140 million and increased operating costs by more than $200 million.

A worker at the Yerkes Plant in Tonawanda, New York, was killed when a 10,000-gallon slurry tank exploded on Nov. 9, 2010. (Photo: U.S. CHEMICAL SAFETY BOARD)
DuPont denied the allegations and countered it was not responsible for cleanup costs because Invista violated a contractual agreement to pay for environmental remediation.
A whistleblower who reported leaks of sulfur dioxide, sulfur trioxide – a carcinogenic – and sulfuric acid mist at the company's Burnside plant in Darrow, Louisiana, filed a lawsuit against the company. Jeffrey Simoneaux alleged DuPont failed to report the leaks for three years.
Simoneaux said plant management retaliated against him for reporting the leaks to the EPA. He was told that he was warned by supervisors not to report the leaks in writing for fear it would create a legal record. Simoneaux also said he was admonished by his bosses for writing the leaks in a company logbook.

Earlier this year, a jury ruled the leaks did not pose a threat to the public and were not large enough to require being reported to the EPA. However, a federal judge vacated the jury's decision. U.S. District Court Judge Shelly D. Dick ruled DuPont withheld crucial information about the leaks and workplace safety standards, calling the company's actions "misconduct."
DuPont has paid $17.2 million to fix damaged equipment at the Burnside plant.
Exceeding industry standards
DuPont officials insist company safety must be judged by the number of productive work days lost to injury. It's a measurement that includes fatalities and is used by the Department of Labor to monitor safety across various employment sectors.
On average between 2007 and 2013, DuPont lost 0.2 days of productivity due to workplace injury. During the same period, the average chemical company lost just under a full work day, according to Bureau of Labor statistics.
DuPont has improved on that number. In 2007, when the Sabine River Works death occurred, the company lost roughly 0.26 days of productivity because of injury. Injuries cost DuPont 0.16 days of productivity in 2013, according to the most recently available Department of Labor statistics.
In 2014, roughly 65 percent of DuPont's plants did not disclose a single reportable injury, according to data from the company. That number has improved since 2003, when just under 50 percent of the plants could claim zero reportable injuries. It peaked at just under 70 percent in 2009, before dropping to 60 percent 2010 and rising every year since.
"Safety is a core value and constant priority at DuPont," Turner said.
Among its peers, DuPont's safety record is favorable. The chemical industry measures safety through its recordable incident rates, a complicated calculation that tracks the number and severity of workplace injuries based on total hours worked. Based on data supplied to The News Journal by the American Chemistry Council and the companies listed, DuPont ranked second in fewest recordable incidents between 2007 and 2014.
Dow reported an average incident rate of 0.24 during the eight-year period. DuPont finished second at 0.75, followed by BASF at 0.77, Honeywell with 0.97 and 3M with 1.47.
Yet other companies recorded fewer fatalities. Neither BASF nor 3M recorded any employee or contractor deaths between 2007 and 2015. Honeywell reported one contractor fatality in 2009, and Dow had one employee die in 2012 and another in 2013.
Some say average incident rates are misleading for the chemical industry, where workers handle hazardous materials.
"Companies calculate that by reporting every tiny injury," Mendeloff said. "But chemical plants with a lot of processes and safety do not have the potential for regular old accidents."
Going forward
Turner said DuPont has taken steps to address the LaPorte incident. He said the company's own investigative team is conducting a "systemic and rigorous" analysis of the leak that killed the four workers.
DuPont is assessing its process safety management system and redesigning its incident reporting system, he said.
The company's reaction to prior incidents has earned praise from the Chemical Safety Board. CSB's Moure-Eraso in 2013 commended DuPont's improvements to its Yerkes plant following the 2010 fatality.
He also commended the company for implementing the same new procedures at all of its U.S. locations, saying he "was extremely pleased" with DuPont's actions.
“The fact they [DuPont] have contested a very modest penalty in the investigation tells me they really don't get it. They have not recognized the severity of the problems.”John Mendeloff, a professor at the University of Pittsburgh, who has written two books on workplace safety
Safety experts expressed concern over DuPont's decision to contest the La Porte fines. Overall, less than 10 percent of the companies fined by OSHA challenge them, Mendlehoff said.
"To some degree, it seems DuPont is concerned about its reputation," he said. "That implies that perhaps they are not facing up to the facts."
Monforton said that shows DuPont is a long way from acknowledging its issues.
"The fact that they have contested a very modest penalty in the investigation tells me they really don't get it," Monforton said. "They have not recognized the severity of the problems."
Fuller disagreed. He said the public relations value of being exonerated of any wrong is worth the legal costs.
"For these big companies, the OSHA fines don't really mean anything," he said. "It's the public relations that makes a difference."